A peek behind the scenes of our sourcing team in China.
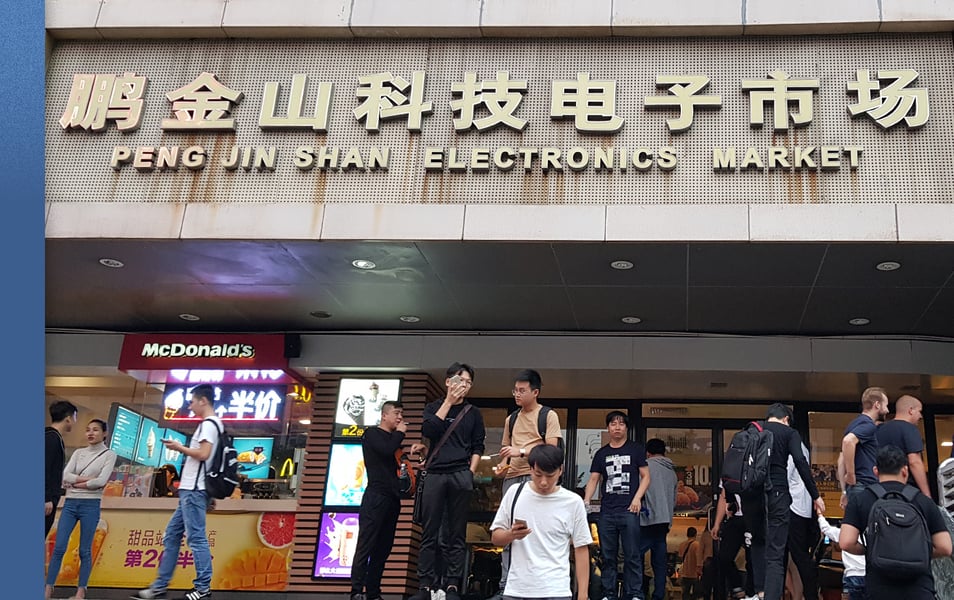
Original parts are available from Samsung, Huawei, Nokia, Sony, LG, Xiaomi, Wiko, Motorola, and OnePlus. This is not the case for iPhone and iPad. Additionally, we also supply refurbished parts for Google Pixel, Xiaomi, Oppo, and OnePlus, among others. To ensure we deliver the best quality parts, we have a fully dedicated sourcing team in Shenzhen (18 FTE). Join us and take a look behind the scenes of our sourcing process, part 1 of 5.
Our Sourcing Team
To ensure we deliver the highest quality, we have stationed our sourcing team in Shenzhen. Shenzhen is home to numerous electronic markets, making it the prime location to source the best quality LCDs and small parts for iPhones, as well as refurbished parts from other leading brands.
The Team
Our team in Shenzhen consists of 18 members in total. Our sourcing manager, Wen, is in charge of procurement, while the remaining 17 members are primarily focused on the quality control process. "We follow a strict control process to weed out any 'bad apples.' This way, we can guarantee the best possible quality."
Meet Our Sourcing Manager from Shenzhen: Wen Hao Qian
"I started at 2Service-Mobileparts.shop as an administrative employee. After a while, I moved to the logistics department. In my spare time, I maintained a website where I imported and sold iPhone parts from China in the Netherlands. This gave me experience in China's electronic market. When 2Service-Mobileparts.shop wanted to expand its range with parts for iPhones and iPads, my father took over this sourcing process. Speaking the language and understanding the culture is a huge advantage for us. It makes the process easier for us to comprehend and effectively manage. When I was still living in the Netherlands, my father handled the processes in Shenzhen. In December 2017, I moved to Shenzhen and took over my father's role. Thanks to my father's and my own knowledge and experience, we can make good agreements with factories, ensuring we receive high-quality products at the right price."
Our Sourcing Process and Advantages
"In the electronic market, you find two types of sellers. First, there are the resellers. These are traders who buy screens from factories and resell them in the markets in Shenzhen. Additionally, the manufacturers themselves are also present in the electronic markets. Approximately 9/10 of the booth holders are resellers.
Sourcing Manager Wen: "I always start a conversation to find out whether the booth holder is a reseller or a manufacturer. I do this by asking various questions about the refurbishment process and inventories. I know someone is just reselling screens by asking simple questions about stock and quality. When someone can't immediately tell me how much of a certain model they have in stock, I know I'm dealing with a reseller and not a manufacturer. When I ask if it's possible to supply a certain component of a specific quality on the screen and the answer is no, then I also know I'm dealing with a reseller rather than a manufacturer."
![]()
![]()
|
![]()
![]()
|
Our Manufacturers
"We do business with manufacturers specialized in certain iPhone series. When a manufacturer specializes in a specific iPhone series, the likelihood of better quality is higher because they have more expertise.
We have more than five fixed manufacturers for our iPhone and iPad parts and LCDs; we prefer not to depend on just one or two. Our manufacturers customize our LCDs for us. Additionally, we are loyal to our manufacturers, which has helped us build a good relationship. Because of this good relationship with the manufacturers, they are aware of our quality requirements. Our fixed manufacturers deliver the small parts or LCDs directly to our office, bypassing the electronic market."
Inventory
"Another advantage is that Mobileparts.shop always wants to have a substantial stock, so I purchase a large volume once a week. This way, our sourcing team can take the time to check all small parts and LCDs and compare them in the market. When there is not enough stock, it must be replenished quickly, leaving less time for quality control."
Controls
"When we find the right parts, they are checked by the sourcing team in Shenzhen. Many companies check the quality on the spot in the electronic market. Here, thorough control is challenging due to the lighting and busy conditions. We always check the parts and screens at a fixed location, ensuring consistent working conditions. Moreover, we check displays three times, whereas others might do it only once. This also explains our low RMA and high customer satisfaction."
If you have a question for Wen in China, feel free to send an email to marketing@2service.nl.
Related articles
-
Parts Shop owner info Future insights Circularity/sustainability
How the Right to Repair and Ecodesign regulations could affect the prices of spare parts.
Discover how new EU rules on Right to Repair and Ecodesign will impact spare parts pricing and repairability scores, making repairs easier and more affordable for technicians.
Read more -
Parts Technical info
What iOS18+ Really Says About An iPhone Display: 'Genuine', 'Used', or 'Unknown'?
Understand the significance of iOS messages when replacing iPhone displays and what to expect with parts from Mobileparts.shop. Discover how Apple tracks component authenticity.
Read more -
Parts Technical info
Technical Warning: Why pre-Installation testing of displays matters
Learn the importance of pre-installation testing for smartphone displays to avoid damage and warranty issues. Ensure functionality before committing to installation.
Read more